Glass Bottle Beer Filling Line: Glass bottles were once the most widely used packaging container in the world. It has particularly good adaptability to the packaging of liquid products. And it is an important packaging material in the food, pharmaceutical, and chemical industries. With the rise of plastic products, the use of glass containers is on a downward trend. In recent years, people have paid more and more attention to environmental protection. Thus glass containers have been reborn. With the continuous development of bottle-making technology, thin-walled lightweight bottles have been promoted and used. For example, the 750ml bottle has been reduced from 600g to 200∽250g. This greatly reduces the cost of beverage manufacturers. And making glass bottle containers more competitive.
1 .What glass bottle should I use for beer filling line?
Glass bottles for food are generally soda-calcium silicon ordinary glass bottles. Beer bottles are usually small-mouth bottles. Small-mouth bottles are further divided into “sloping shoulder bottles” and “flat shoulder bottles”.


In China, there is a industry standard for small-mouth bottles. 6 sizes of nominal capacities: 125ml, 250ml, 350ml, 500ml, 640ml, 750ml. Only 350ml and 640ml are available for carbonated beverages. The remaining specifications are for non-carbonated beverages. If you want to purchase glass bottles from China, be sure to check with the glass bottle manufacturers above details.
2 .How should the cap be chosen?
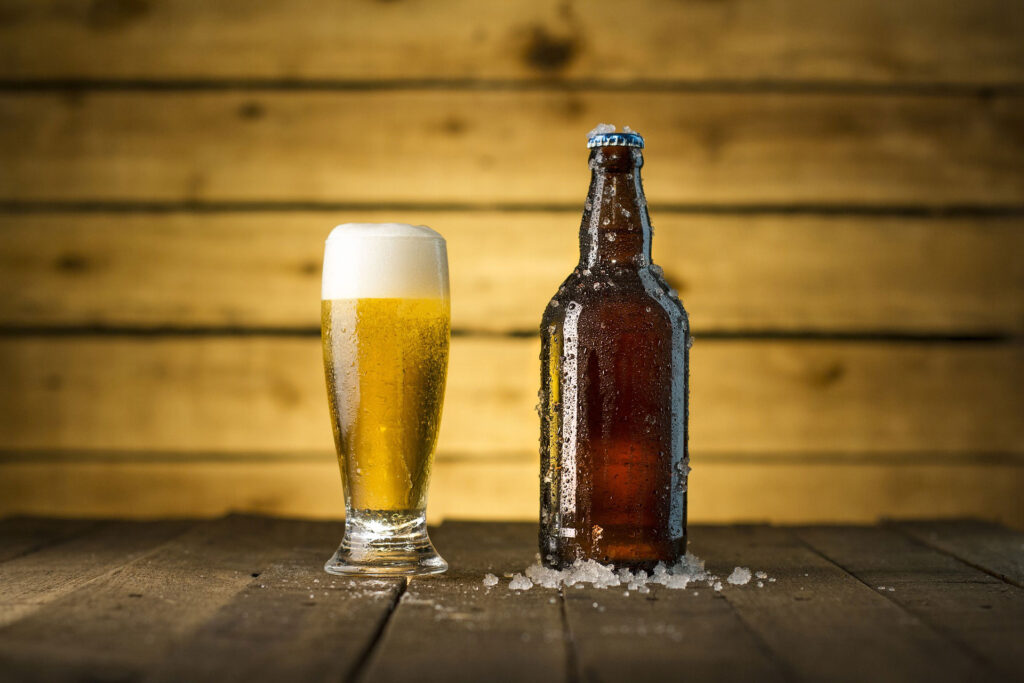
The capping forms of carbonated drinks are crown caps and aluminum caps. The crown caps are machined from tinplate and lined with plastic gaskets. Mostly used in beer packaging. Aluminum caps are more common in sparkling water. You can visit the local market to see which cap is more popular.
3 .What is the packaging process for glass bottle beer filling line?
The packaging process for bottled beer is as follows:
Bottles Cleaning- Filling – Capping – Sterilization – Inspection – Bottle Drying – Labeling – Boxing
Next, we will introduce the packaging process of the entire bottled beer filling line in steps.
1) .Bottle Cleaning
How is a glass bottle made?
The raw material of glass bottles is mainly quartz sand. Quartz sand and other excipients are mixed in a certain proportion. The mixture is heated at a high temperature of 1550-1600 celsius degrees to form liquid glass. Liquid glass is then injected into the mold to form bottles. Finally, a series of cooling processes are used to complete glass bottles.
Buy new bottles from glass bottle manufacturers. Bottle rinsing machine rinse bottles before filling. You can choose a separate rinsing bottle machine, or you can choose a rinsing, filling, capping three-in-one combination machine. The combination machine is faster and occupies a smaller space.
Besides purchasing new bottles, many manufacturers will also recycle bottles for use. After the recycled bottle selection, it needs soaking and washing. This work is mainly done by recycle bottle washing machine.
The cleaning process of the bottle is as follows:
Bottle input – soaking and rinsing – bottle internal brushing – bottle inner rinsing – drain – bottle output
Soaking and rinsing.
Bottle enters the soaking machine. The spray pipe group pre-sprays the inner and outer surfaces of the bottle to make the bottle evenly heated. Then, perform the following procedure:
High-pressure spray bottle inside and outside – pour out the sewage in the bottle – soak – pour out the sewage – bottle output.
Cycle 3-4 times, after such treatment of the bottle, the logo and dirt have been removed.
Waste label filtration and Alkaline water circulation
When the bottle enters the inner brushing draining machine, it rotates intermittently with the drum. When the bottle is in a horizontal position, the high-speed rotating brush is driven into the bottle to brush bottles. When the brushing is complete, the brush exits. The drum is turned at an angle, and a row of rinser rinse bottle inside with tap water. When the bottle is in a vertical downward position, another row of rinser rinse bottle inside automatically. And then bottle turns into the drainage section. After draining, the clean bottle is sent out.
Bottle inner brushing, rinse and drain.
After the bottle enters the inner brushing draining machine, it rotates intermittently with the drum. When the bottle is in a horizontal position, the high-speed rotating brush is driven into the bottle to brush bottles. When the brushing is complete, the brush exits. The drum is turned at an angle, and a row of rinser rinse bottle inside with tap water. When the bottle is in a vertical downward position, another row of rinser rinse bottle inside automatically. And then bottle turns into the drainage section. After draining, the clean bottle is sent out.
Throughout the bottle washing process, the soaking solution should be efficient, low foam, non-toxic. Alkaline cleaning fluids are commonly used. Such as 3% of the aqueous solution of NaOH. The soaking temperature is up to 65-70 celsius degrees. Minimum not less than 55-celsius degrees. The rinsing pressure is 0.2-0.25Mpa.
2) .Filling Capping
Cleaned and drained bottles are transferred by the conveyor system to the filling machine. As mentioned earlier, we generally use a rinsing filling capping three-in-one machine. In this way, bottle rinsing, beer filling and capping can be achieved on one machine.
Size of the filling machine is divided into small and medium sized according to the number of filling heads. Small to medium sized fillers are 6-24 heads, large fillers are 40-70 heads. Speed is from 10-200 bottles / min.
Technical conditions for beer filling are as follows:
- The filling temperature is controlled at -1∽3 degrees. In case CO2 escapes from beer.
- Beer filling uses counter-pressure filling technology. in the article “HOW TO CHOOSE A FILLING MACHINE FOR ALCOHOL DRINK?“, we detail the filling steps of the glass bottle beer filling machine. Please click to view.
3) .Beer Filling Line Sterilization

In order to extend the shelf life of beer, the beer needs to be pasteurized. In the article “Canned Beer Filling Line“, we have introduced it in more detail. You can click to see. The sterilization process of glass bottle beer is basically the same as that of canned beer. But there are some differences.
- There should be 3%∽4% of the remaining space in the bottle. Beer must not be full filled.
- The sterilization temperature is generally 65 celsius degrees. Keep on hold for 10∽15 minutes.
- The temperature difference between hot water and beer should be maintained at 2∽3 celsius degrees. To prevent partly overheating.
- Heating up and cooling should be moderated. In case the bottle breaks.
4) .Beer filling line Inspection
Before labeling, sterilized bottled beer needs to be inspected. Mainly to see whether the beer is clear and transparent, free of suspended solids and impurities. The cap does not leak beer. The upper gap height is maintained at 6-8cm. There is nothing dirty on the outside of the bottle. Manual sampling or high-speed inspection machines can be used. High-speed inspection machines are generally used in high-speed production lines.
5) .Blow Dry Machine


After the spray sterilization machine, the bottles that come out of the tunnel need to be blow-dried with a blow dryer. To carry out the next production, Linho uses a spider-foot blow dryer. All blower angle is adjustable. The angle of blow-drying can be adjusted according to the height of the bottles.
6) .Labeling machine


Glass bottles are more commonly used to resist moisture and alkali paper label. Paste with the label sticker. The label panel are generally the neck, bottle front and bottle back. You can choose one label, two or three labels according to your promotional needs.
7) .Date Printer
There are ink type and laser type for date printer. The same efficiency of the date printer, ink is cheaper than laser. The difference can be as high as $10,000. The inkjet head of ink type need to be cleaned to prevent it from clogging. And it required consumption goods such as ink . Laser type seems to be more suitable for areas where purchasing consumables is inconvenient. Laser coders require almost no consumption parts and have few problems. Apart from being expensive, it has few drawbacks. Laser coders are more used in China. Next time you go to the supermarket, you can observe. Which coder type is more common in your country.
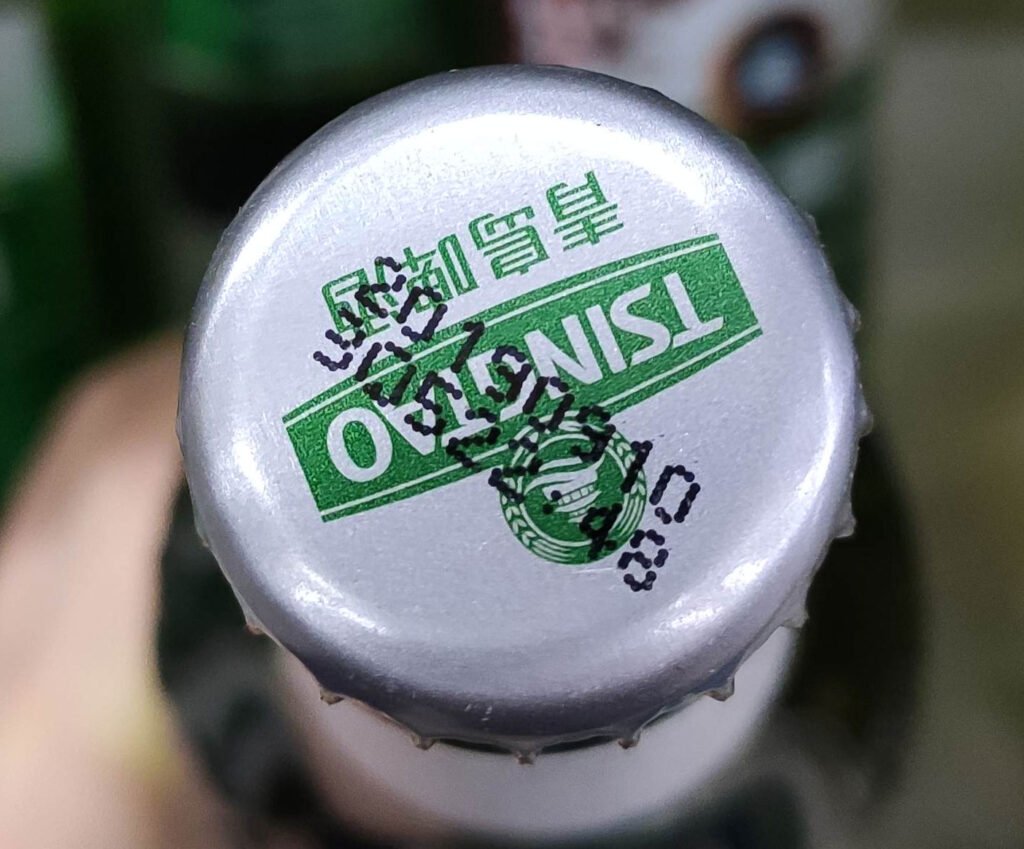

The most popular coder brands on the market today are Linxin from UK, Imajet from France, Videojet from US. Made-in China are more used in China. This mainly benefits from its excellent cost-effectiveness.
Common glass bottle packaging methods on the market are mainly carton packaging. In the article “How to choose the rear packaging machine“, we have detailed the glass bottle most commonly used as a grapping cartoning machine. Please click to view.
From raw materials such as bottles, caps, labels, to filling machines, packaging machines, Linho can provide you with professional advice and design. If you are planning to build a glass bottled beer filling line, please contact us to know more about the glass bottled beer production line!